How to Save on Non-Warranty Service Calls
August 12, 2022
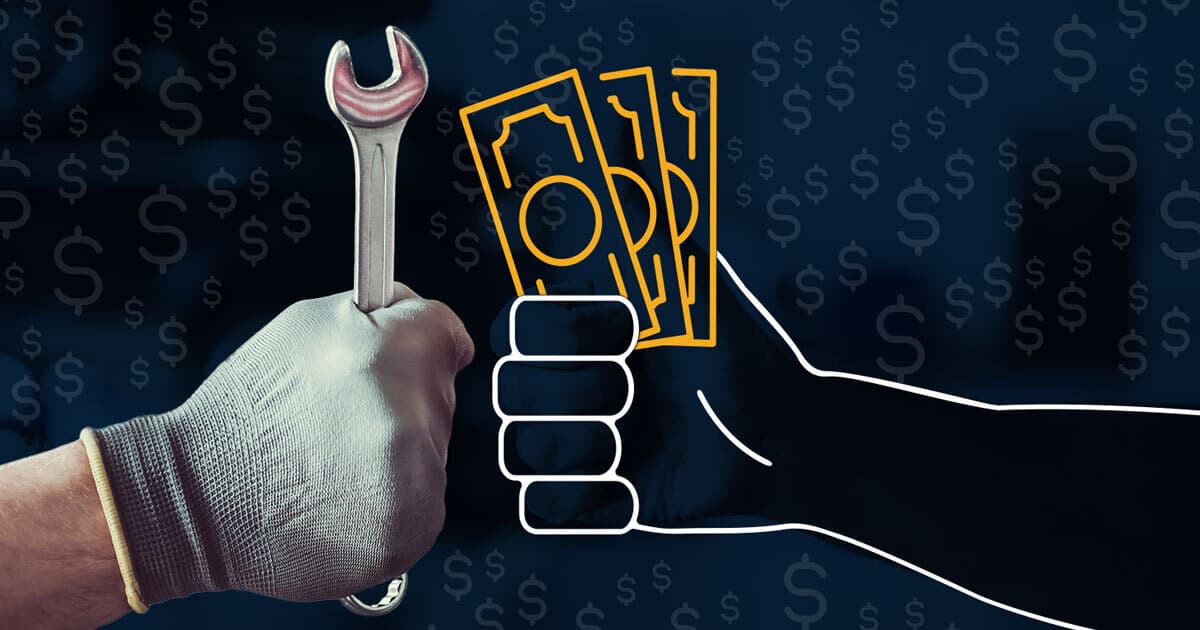
As the bevy of complications facing the foodservice industry continue to mount, service companies face ever-rising costs, labor and equipment shortages, and harsh reality checks to bottom lines. Finding ways to reduce costs and sharpen efficiencies is increasingly important to maintain profitability. Although we can't control the markets or the supply chain, there are things service companies can do to trim costs and boost profits in other ways.
Utilize OEM-equivalent parts when servicing equipment.
OEM equivalents are often manufactured in the same plant as their OEM counterparts, using the same materials and processes. They may look a little different, but they function in the same way as OEMs.
Mavrik-brand OEM equivalent parts are required to meet strict quality standards and receive the same certifications as OEM parts. In addition, they are backed by a 180-day warranty. Studies have found that Mavrik parts are an average of 29% cheaper than OEM parts, equaling an average savings of $12.85 per part. Over time, 29% can provide a health boost to profits!
Carefully plan your truck inventory.
What technicians can have on their trucks for service calls can make or break efficiency. OEM equivalent parts allow you to carry a lot more inventory because one equivalent fits a variety of makes and models.
Allpoints' Truck Stock program enables each technician to increase first-time fix rates. An organized set of tools and replacement parts helps avoid extra trips for forgotten materials. Having these items on hand allows technicians to take on as many service jobs as possible.
Make use of technology to streamline and standardize your service processes.
From the call center to the job site, there are many ways to utilize the technology to increase your efficiency. These include:
- Instituting remote assistance for technicians with digital tools like EquipID.
- Utilizing GPS tracking to pinpoint technician locations and where to direct them for the next assignment.
- Employing digital invoicing systems to eliminate paperwork.
- Standardizing one system of measurement to track the efficiency of each call.
- Documenting calls to systematically determine if inefficiencies exist and narrow in on areas that can be improved.
- Adopting first-time fix rate as a standard KPI.
- Measuring individual technician efficiency and establish goals, as well as daily and weekly targets, and determining where additional training may be needed.
Although we may still be navigating very uncertain waters, there are still ways to improve the efficiency of non-warranty calls — ways that might have been overlooked under better industry circumstances. If service companies improve in these areas now, they can be better positioned for healthy jumps in profitability when the tides turn and the issues plaguing the foodservice industry resolve.