Repair vs. Replace: Foodservice Equipment Considerations
January 26, 2021
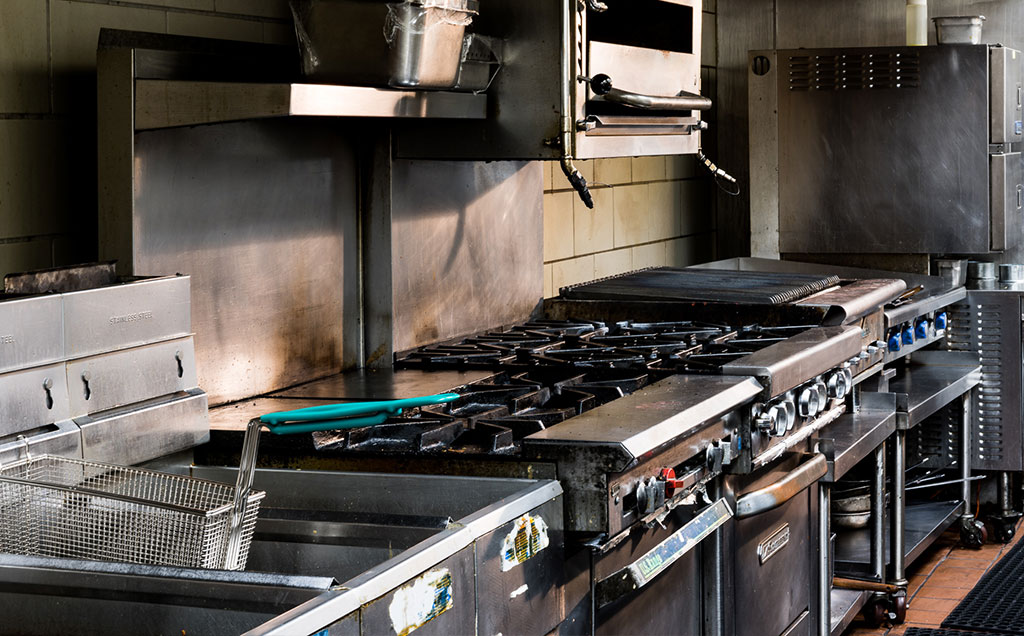
For all foodservice organizations, equipment is vital to preventing devastating downtime and keeping operations running smoothly and consistently. After a tough year for the foodservice industry, operators are often faced with the difficult decision to repair or replace broken equipment. Operators will often reach out to dealers and service agents for advice on what decision to make. Dealers and service agents alike have a responsibility to make the best recommendation they can to their customers.
Dealer perspective
Dealers are often more familiar with customers' operations than manufacturers. They understand the ins and outs of how the equipment is used as well as volume and operating hours — two key pieces of information for helping to guide operators in this decision. Additionally, they have experience with different types of equipment in various scenarios and can draw on that experience to make an informed recommendation to operators.
Service agent perspective
Service agents have a valuable perspective on equipment as well. Those with established relationships will have a record of all performed maintenance on operators' equipment going back several years. Those records will help to answer many questions regarding a piece of equipment's overall condition, another significant piece of the puzzle in helping make the best decision regarding replacement or repair.
Repair vs. Replace Considerations
As both dealers and service agents make recommendations on whether to repair or replace broken foodservice equipment, here are several considerations they should keep in mind.
Safety
Safety will always be a top priority for operators and should always be the first factor studied. A piece of equipment that is not working properly can threaten both the wellbeing of kitchen staff as well as the quality and safety of the food prepared. If a repair will renew the safe operation of the equipment, consider the best repair option as recommended by the service technician. If a repair cannot restore safety, replacement is the only option.
Efficiency
An inefficient piece of equipment can affect a significant budget loss, leading many to believe it's time to replace. However, there are many energy-saving options that can be installed to extend the life of the equipment and improve efficiency. These low-cost/high-impact fixes carry the added bonus of helping. build trust and customer satisfaction for dealers and service technicians. Worn gaskets, for example, can be detrimental to energy efficiency and are often easily replaced for an efficiency boost. As operators face many difficult financial decisions, exploring energy-saving options can help stretch equipment budgets.
Parts availability and cost
Another factor that often forces operators to consider replacement is the scarcity of replacement parts for older equipment models. While parts availability can be a legitimate predecessor for equipment replacement, many operators are unaware, however, of all the parts options they have at their disposal. AllPoints, for example, has sourcing specialists on staff who can help track down hard-to-find parts that can save operators the need to replace otherwise well-functioning units.
Availability isn't the only parts factor to consider. Some replacement parts can be so costly that it's almost worth it to replace the equipment. For these and all replacement parts, service agents can save operators money by using OEM equivalents. AllPoints OEM Equivalents™ are often manufactured in the same factory as OEM parts and are much more cost-efficient than OEMs but with the same quality and reliability.
Cost
Cost is almost always an underlying motivation for the repair vs. replace debate and will probably be the most important factor as operators consider their decision. Calculating the cost of whether to repair or replace isn't simple, however, as there are many different components to take into account.
Replacement costs, for example, aren't as straightforward as negotiating a buying price. Here's what operators have to factor in for replacement:
- New equipment cost
- Old equipment removal from utilities charges
- Old equipment hauling and disposal fees
- New equipment installation and calibration charges
- New equipment training overhead
All costs associated should be included when discussing the cost of repair vs. replace with operators, as this will often be the driving force for the decision.
Moving forward
This year will be a tough one for foodservice operators as they recover from pandemic-related strains. It's up to dealers and service agents to provide them with advice on how to ensure their equipment budgets are maximized in the wisest and most appropriate ways. These considerations will help guide you in making the best possible recommendations to operators.
Need some advice on parts costs for specific equipment repairs? Reach out to our customer service team for their expert assistance.