Why Service Technicians Are Switching to OEM-Equivalent Parts
April 18, 2022
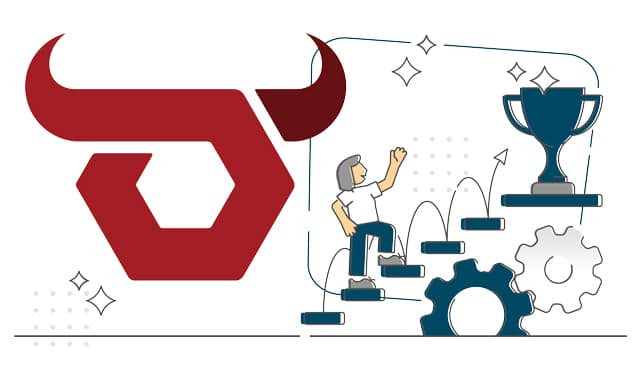
For decades, the foodservice industry has been dependent on equipment manufacturers for parts and supplies. But a change is on the horizon, with more and more service technicians switching to using OEM-equivalent parts.
Service technicians and parts dealers have long been subject to OEMs' high prices and limited availability, making them ready to turn to OEM equivalents for more options. The main reasons they're making the switch to OEM-equivalent parts? Equal quality, better availability and lower costs.
OEM equivalent quality
In the past, service techs have been hesitant to choose OEM equivalents because they believed OEM equivalents were inferior to OEM parts. However, those who have made the switch to OEM equivalents are quickly finding that OEM equivalents are equal to - or in some cases, better than - their OEM counterparts.
As long as service techs are purchasing their OEM-equivalent parts from a reputable company with a reliable warranty, they're finding OEM equivalents to be equal to OEMs in quality and reliability.
OEM equivalent availability
Another factor that attracts service agents to OEM-equivalent parts is their availability. In the world of foodservice equipment repair and maintenance, having the parts needed available immediately for any issues makes a significant impact on repair time, first-time fix rates and the agency's reputation.
OEM-equivalent parts are often more readily available than OEM parts - and have the bonus of being versatile, not dependent on the equipment brand. Service technicians have found they can, for example, keep OEM-equivalent magnetrons on hand that can be used in almost any microwave, regardless of the OEM brand.
OEM equivalent cost
While the industry is certainly bouncing back from the struggles that came during the past couple of years, cost is still a high motivator, and the significant cost savings that comes from switching to OEM-equivalent parts is persuasive.
OEM-equivalent parts are often far more cost effective than OEMs because they don't carry the equipment brand name and aren't limited by the layers of overhead costs many OEMs are required to include.
How Mavrik™ is leading the way for OEM equivalents
Mavrik™, a new brand of OEM-equivalent parts, is a great example of a reliable OEM-equivalent backed by AllPoints' dependable reputation.
Mavrik quality
At AllPoints, we have a long-held reputation of sourcing quality OEM-equivalent parts. Our team of global sourcing experts works hard to ensure Mavrik parts are made with the highest quality parts available. In fact, Mavrik parts are often made in the same manufacturing facility as their OEM counterparts, using the same materials.
Mavrik OEM-equivalent parts go through rigorous testing and must meet strict quality standards, often coming with industry-recognized certifications.
Mavrik parts backed by an industry-leading 180-day warranty, double the standard 90-day warranty most OEM parts come with. They have a risk-free 90-day hassle-free return policy, allowing service agents and dealers to return any Mavrik part for 90 days with no restocking fee.
Mavrik availability
We have invested a significant amount of time and money into ensuring Mavrik parts are in stock and ready to ship. Several local distributors and dealers have Mavrik OEM-equivalent parts in stock for easy, same-day purchases. All this to provide service technicians with more parts options.
Mavrik costs
One of the most attractive qualities of Mavrik parts is the cost savings they afford service technicians. Although the exact amount of cost savings shifts from part to part, Mavrik parts are, on average, 29% less expensive than OEM parts, with a difference per part of $12.85.
These savings add up over time and can help service agencies increase their bottom line considerably.
Learn more about Mavrik and make the switch to OEM-equivalent parts today. You won't regret it